It’s vital that the 2.3-million South Africans who ride trains every day reach their destinations safely. Flow Communications is helping to make that happen.
We recently visited the manufacturing plant of one of our newer clients, Gibela, in Dunnottar on the East Rand, where it is building trains to replace our country’s ageing urban commuter fleet. Gibela has been contracted by the Passenger Rail Agency of South Africa to build 600 trains – comprising 3 600 passenger cars – over 10 years. Each of the trains is designed to carry 1 200 passengers.
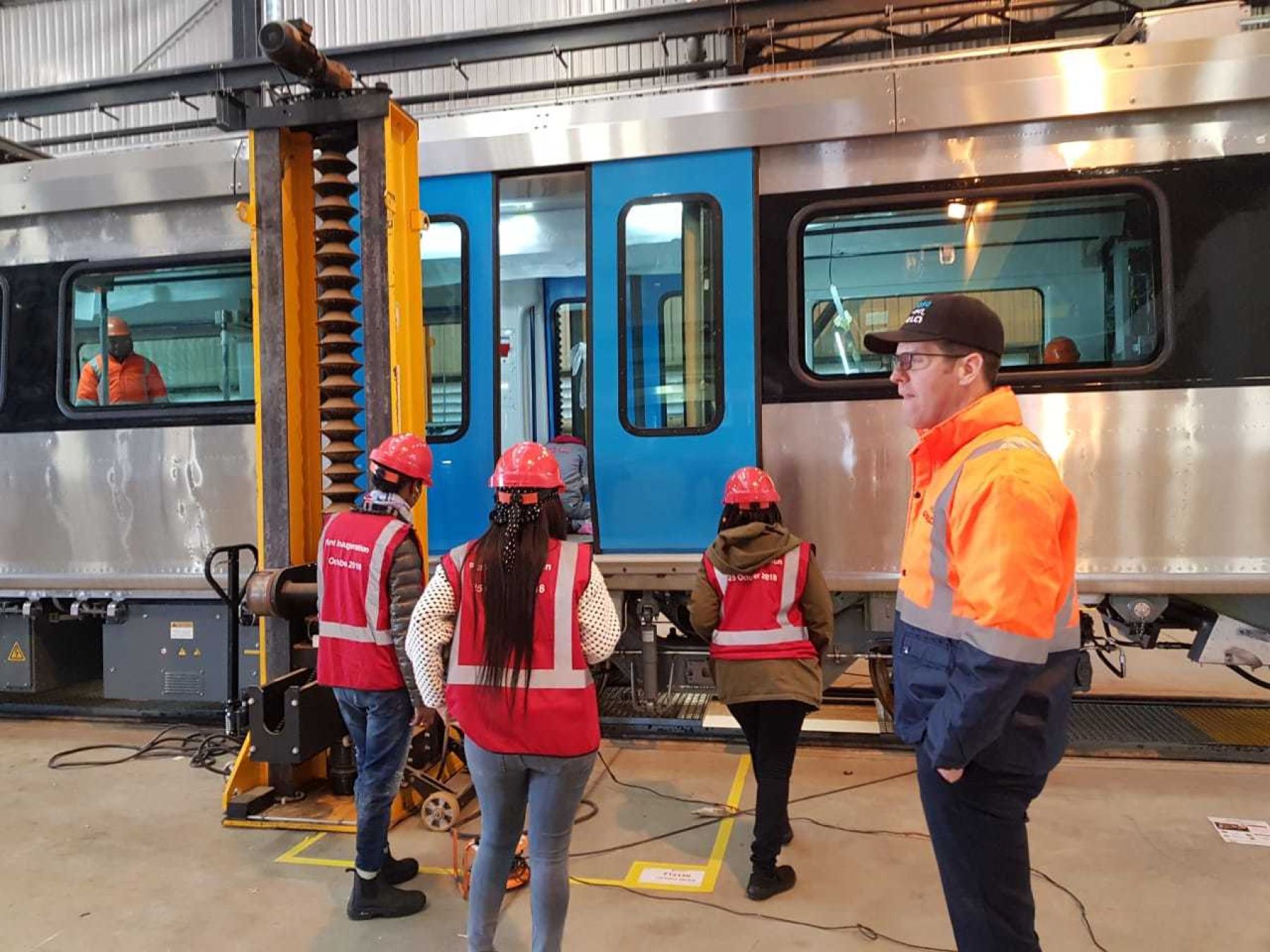
Gibela has enlisted Flow’s assistance with an internal communications campaign around quality control, to ensure that the trains it produces meet the highest quality and safety standards.
Finding out what goes into building South Africa’s next-generation commuter trains was fascinating. For example, manufacturing a train car takes eight stages – from building sub-assemblies to putting the entire car together, and checking that everything works properly and that the vehicle doesn’t leak.
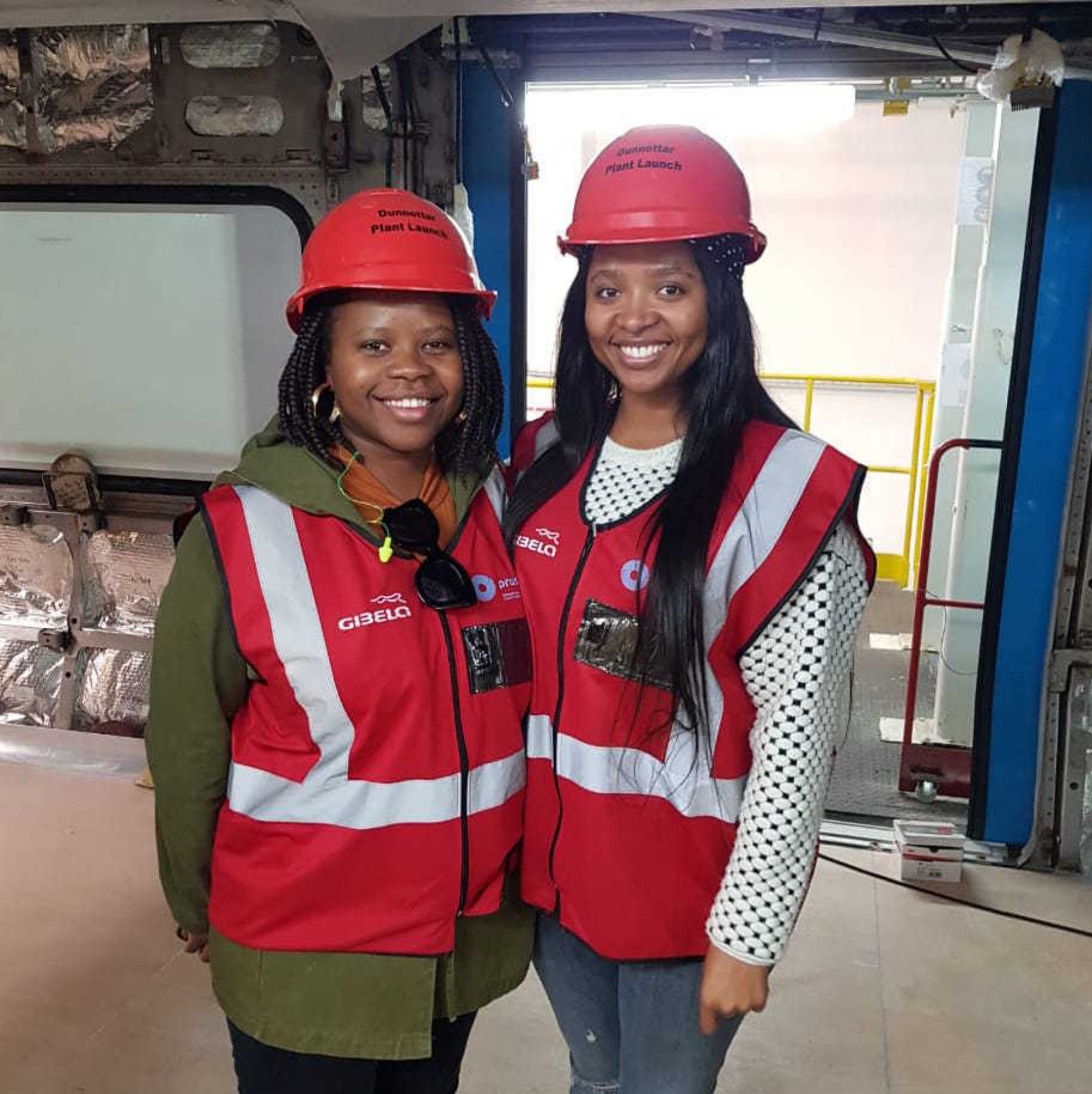
Each car is made of 100% South African steel, and comprises 3 000 components – including 1 400 fabricated by Gibela. They contain 30 000 cables totalling 100km in length. Much of the construction is done by robots, which perform 1 000 welds an hour, with the rest completed by humans.
Once the cars are constructed they are tested to a maximum speed of 60km/h on Gibela’s 12km-long test track. The trains are later tested at higher speeds on commuter lines.
Once the factory is up to speed, every day two train cars will roll off the Gibela production line, and every month three train sets of six cars each – 131m in length and weighing 145 tons – will be completed.
The design being produced at Dunnottar is the X’Trapolis MEGA, a state-of-the-art train developed to accommodate South Africa’s 1.067m gauge rail tracks.
But these are quite unlike the commuter trains we know right now. Each car boasts several modern features, including wide double doors for easy access, spacious interiors, air conditioning, Wi-Fi access, CCTV security and, in some cases, toilets.
Safety is an integral part of the design, which is compliant with all the latest international requirements, including an anti-crash system that is designed to protect the driver and passengers in a collision.
But safety begins on the factory floor, with the actual manufacture of the train cars. In this, Flow is poised to play an important role in inculcating quality control among staff, in every step of the manufacturing process.
It’s a big responsibility – especially when you consider that South Africa’s rail commuters are expected to double in number in the next two decades.